GOALS
The Consorzio is open to all entities involved in the various stages of the Production Supply Chain for accessories bound for the Fashion and Luxury sectors – ranging from process material suppliers up to companies specialized in industrial plants, accessory production and finishing treatments. The Consorzio primary goal is to reduce the environmental impact across the entire Supply Chain, by supporting projects and initiatives aimed at:

The implementation of new technologies for surface treatment of metal accessories
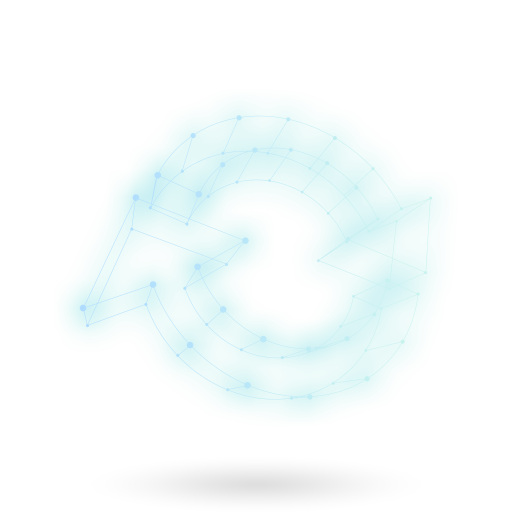
The reuse of metals as secondary raw materials
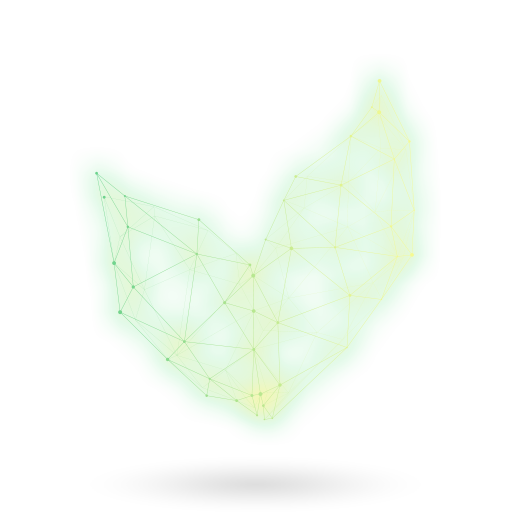
The development of innovative base materials with reduced environmental impact
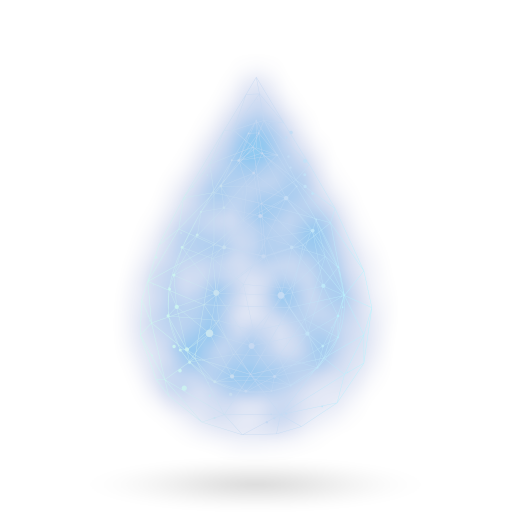
The refinement of new technologies for treating process wastewater

The implementation of new technologies for surface treatment of metal accessories
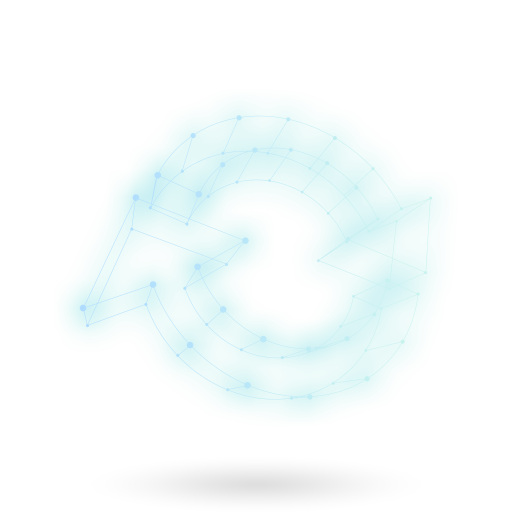
The reuse of metals as secondary raw materials
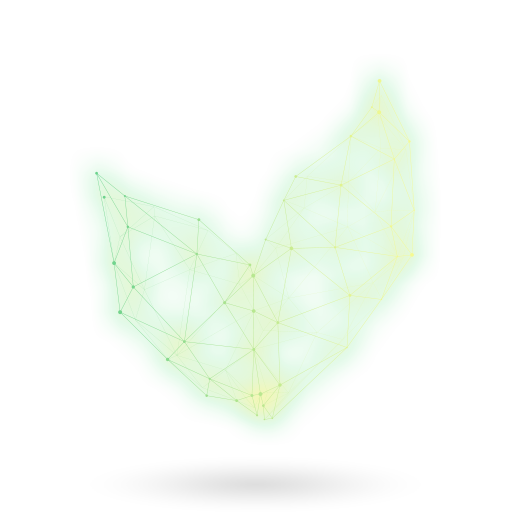
The development of innovative base materials with reduced environmental impact
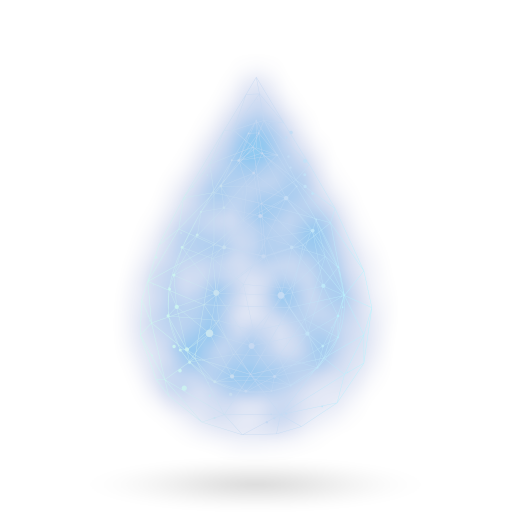
The refinement of new technologies for treating process wastewater
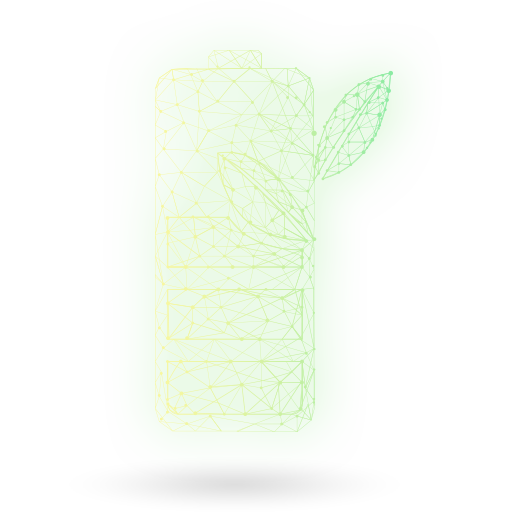
The reduction of water consumption and impacts related to the use of treatment water in galvanic plants
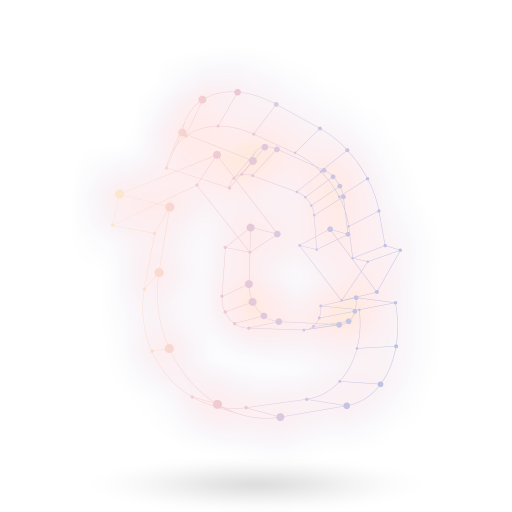
Metal recovery
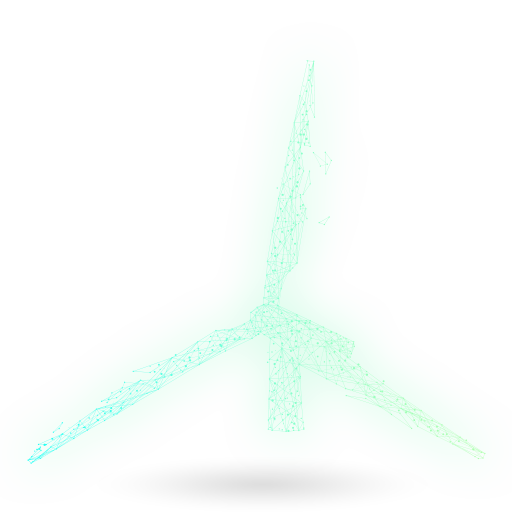
The development of plants with innovative solutions for optimizing energy consumption in production processes
PROJECTS
Companies and stakeholders in the Supply Chain can find in the Consorzio the ideal partner for the development of innovative and sustainable projects specific to their sector, including by way of example:
The development of brass and bronze alloys from recycled materials for the production of metal accessories, by making use of hot stamping, investment casting, and CNC applications. The determination of the physical-mechanical properties of the resulting alloys and the performance of comparative assessments as regards corrosion resistance of the produced accessories as compared to those made from virgin raw materials.
Research of new techniques for energy saving in galvanic plants through the development of alternative energy recovery systems, as well as implementation of comparative LCA (Life Cycle Assessment) analyses between traditional and newly developed systems, cost analysis, and investment assessments.
Development of projects for metal recovery and their subsequent recycling and reuse in galvanic electrodeposit processes. Evaluation and assessment of the chemical-physical properties of the plating baths achieved by using recycled components and assessment of their impact on the corrosion resistance of the produced accessories and on the long-term stability of electrolytes in time.
Reduction of the use of cyanide-based products in galvanic plants through the development of galvanic electrodeposition solutions with lower content of hazardous substances. Carrying out of deposition tests on accessories in pilot lines as well as in industrial production lines, with the support of comparative testing of the durability of the produced accessories versus the durability in case of the use of traditional galvanic plating baths as well as use stability analysis of the developed solutions.
Use of recycled copper wire for galvanic applications, particularly for the use of the above mentioned wire for the binding of items subjected to electrodeposit in connection with their use in galvanic plating/dipping baths. Determination of technical specifications, as well as of mechanical, and chemical resistance.
Identification of new washing techniques in order to reduce water consumption within galvanic plants (development of new washing methodologies aimed at reducing the volumes of water used for rinsing in galvanic plants) and carrying out of comparative tests with traditional washing methods, that are evaluated through LCA – Life Cycle Assessment.
More efficient metal recovery and reduction of load on wastewater treatment plants in order to optimize impacts, by making use of comparative tests compared with traditional systems and LCA analysis.
The development of brass and bronze alloys from recycled materials for the production of metal accessories, by making use of hot stamping, investment casting, and CNC applications. The determination of the physical-mechanical properties of the resulting alloys and the performance of comparative assessments as regards corrosion resistance of the produced accessories as compared to those made from virgin raw materials.
Use of recycled copper wire for galvanic applications, particularly for the use of the above mentioned wire for the binding of items subjected to electrodeposit in connection with their use in galvanic plating/dipping baths. Determination of technical specifications, as well as of mechanical, and chemical resistance.
Research of new techniques for energy saving in galvanic plants through the development of alternative energy recovery systems, as well as implementation of comparative LCA (Life Cycle Assessment) analyses between traditional and newly developed systems, cost analysis, and investment assessments.
Identification of new washing techniques,in order to reduce water consumption within galvanic plants (development of new washing methodologies aimed at reducing the volumes of water used for rinsing in galvanic plants) and carrying out of comparative tests with traditional washing methods, that are evaluated through LCA – Life Cycle Assessment.
Development of projects for metal recovery and their subsequent recycling and reuse in galvanic electrodeposit processes. Evaluation and assessment of the chemical-physical properties of the plating baths achieved by using recycled components and assessment of their impact on the corrosion resistance of the produced accessories and on the long-term stability of electrolytes in time.
More efficient metal recovery and reduction of load on wastewater treatment plants in order to optimize impacts, by making use of comparative tests compared with traditional systems and LCA analysis.
Reduction of the use of cyanide-based products in galvanic plants through the development of galvanic electrodeposition solutions with lower content of hazardous substances. Carrying out of deposition tests on accessories in pilot lines as well as in industrial production lines, with the support of comparative testing of the durability of the produced accessories versus the durability in case of the use of traditional galvanic plating baths as well as use stability analysis of the developed solutions.